為了摸清中國餐廚廢油現狀,消除環境污染,保障人民飲食,通過跟蹤調查,我們研究了中國城市餐廚廢油的產生現狀、危害,并對目前現有餐廚廢油資源化技術進行了系統分析。分析結果表明,中國餐廚廢油產生量大面廣,容易造成較為嚴重的環境風險和健康威脅。現有餐廚廢油資源化技術主要包括生產生物柴油技術、生產硬脂酸和油酸技術、生產肥皂或洗衣粉技術、生產潤滑油技術、生產混凝土制品脫模劑技術等。
餐廚廢油包括煎炸廢油、泔水油和地溝油等源自于餐飲業的廢油脂,成分主要是烹調用植物油和食品中動物油脂,化學組成主要為脂肪酸甘油酯。其中,煎炸廢油來自于餐飲業的煎炸工序,由于反復高溫煎炸,容易產生具有致癌作用的脂肪酸類聚合物,這類廢油產生源相對集中,容易收集。泔水油主要是指從餐廚垃圾中分離回收的廢油,這類廢油是植物油和動物油的混合物,主要來自餐廚垃圾處理廠,容易收集和集中管理。地溝油是從下水道或飯店隔油池中獲取的廢油脂。
地溝油中含有大量污水中的飄浮物、飯店沖洗碗筷使用的表面活性劑等,并極易酸敗變質、滋生霉菌,產生致癌物,這類廢油在三種廢油中衛生狀況差,一般由小商販私下收集后賣給加工商。
餐廚廢油具有鮮明的廢物和資源的二重性,需要進行無害化處理和資源利用。在目前管理體系相對不完善的形勢下,由于利益驅使,餐廚廢油極易被不法商販加工為食用油重新回到餐桌,嚴重威脅居民健康。尤其是在夏季大排檔和路邊攤等餐飲點存在較大監管難度,摻加了廢油產品的食用油容易進入食物鏈。
因此,在充分研究中國餐廚廢油產生現狀及其環境風險和健康風險的基礎上,通過法律手段、行政手段、經濟手段相結合,正確引導餐廚廢油物流路徑,控制廢油出口,并采用合理可行的工藝技術,將餐廚廢油深加工為高附加值的化工原料,從而消除環境污染,實行資源利用,對于保障人民身體健康、發展循環經濟具有重要意義。
1
中國餐廚廢油產生現狀
改革開放以來,我國國民經濟長足進步,城市人口迅速增長,人民生活水準不斷提高,城市餐飲業日益繁榮,使餐廚廢油的產生量增長。
研究表明,餐廚廢油的產生量約為餐廚垃圾產生量的10%-20%,不同經濟水平和餐飲習慣的地區略有區別。2006年我國全國城市餐飲業零售額超過1萬億元,2017年全國城市餐飲業零售額達到39643.7億元,而且平均每年以10.7%的速度增長。
這筆消費中,約20%-30%為餐廚垃圾和餐廚廢油付了帳。以城市人口平均每人每天產生餐廚垃圾0.1kg計算,2015年末全國城鎮人口7.21億,加之外來人口,增長約20%-40%,城鎮人口總計可達約9.3億,則全國城鎮年產餐廚垃圾4000多萬噸,餐廚廢油400多萬噸,加上肉聯廠下腳料及動物內臟提煉的動物脂肪和廚房抽油煙機集油槽收集的廢油,餐廚廢油的產生量仍會增加10%左右。
目前,北京市每天產生的餐廚垃圾約2500 噸、餐廚廢油約300噸,其中地溝油約100噸、煎炸廢油和泔水油共約200噸。蘇州市1000多家大型飯店餐廳及1000多家企、事業食堂,每天餐廚垃圾產生量400 t/d以上,餐廚廢油約60噸,其中地溝油約30噸,煎炸廢油約15噸,泔水油約15噸。
在江蘇省蘇州市吳中區取樣對三種餐廚廢油成分進行測定,部分指標平均值如表1所示。
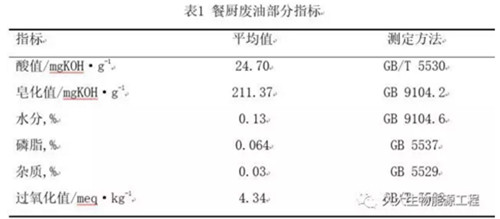
餐廚廢油主要組成元素為C、H和O,屬于大分子疏水性有機物。由于經過反復高溫煎炸,油脂中的小分子營養物大部分已揮發或聚合成大分子熱穩定性物質,可生化性能較低,且含有一定量的苯并芘等致癌物,進入環境或被人體攝入,將造成嚴重的環境污染和健康威脅。具體表現在如下幾個方面:
01
污染水體
餐廚廢油是重要的營養性水體污染物之一,進入水體會造成水質惡化和富營養化,并使污水處理廠生物處理單元處理效率顯著降低。
02
散發臭氣
餐廚廢油,尤其是地溝油,在空氣中曝露時間很長,發生氧化酸敗,散發揮發性脂肪酸類惡臭氣體,嚴重影響環境,是引發公眾強烈反應的主要原因之一。
03
造成食品問題
由于餐廚廢油經過反復高溫煎炸,容易生成苯并芘、反式脂肪酸等對人體有害的物質,廢油在空氣中長期曝露,容易氧化酸敗,產生大量毒素。在物流過程中容易混入有毒有害物質,滋生黃曲霉等細菌,產生具有強致癌作用的黃曲霉素等,一旦處理不當,重新進入食品鏈,將會嚴重影響人類健康,甚至可能造成重大食品事故。
3
餐廚廢油資源化技術現狀分析
目前國內外關于餐廚廢油資源化處理技術的報道較多,主要包括利用餐廚廢油作為化工原料生產生物柴油、硬脂酸和油酸、肥皂、潤滑油、混凝土制品脫模劑等產品的工藝技術,這些技術在實際中均有應用,并取得了一定的效果。
01
生物柴油生產技術
利用餐廚廢油脂生產生物柴油,常用的生產方法為預酯化-二步酯交換-酯蒸餾工藝。其流程為:經預處理的油脂與甲醇一起,加入硫酸作催化劑,在60 ℃常壓下進行酯交換反應,生成脂肪酸甲酯(即生物柴油)。由于化學平衡的關系,在一步法中油脂到甲酯的轉化率僅達到96%。
為超脫這種化學平衡,通常采用二步反應,即通過一個特殊設計的分離器連續地除去初反應中生成的甘油,使酯交換反應繼續進行,可獲得高達99%以上的轉化率。然后,加入少量NaOH進行中和,去除多余的酸。由于堿催化劑的作用生成了肥皂,色素和其它雜質混合在少量的肥皂中,產生一深棕色的分離層,在分離操作時將其從酯層分離掉。通過這種精制作用可以高轉化率獲得淺色的脂肪酸甲酯。這里面重要的一步反應是酯交換,反應過程如圖1所示。
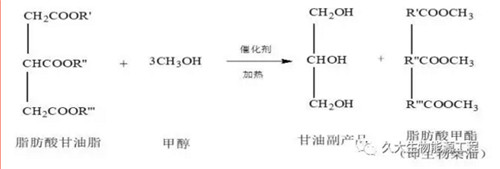
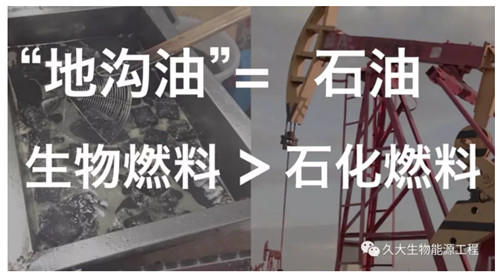
硬脂酸和油酸生產工藝
餐飲廢油中含有大量硬脂酸和油酸,經工業提取分離后大量地應用于日用化工、紡織、醫藥、化學、建材、食品等行業中。其生產工藝主要是通過對油脂水解后,分離出各種脂肪酸(主要為硬脂酸、油酸)。其中油脂水解的方式大致分為常壓下皂化分離和高壓酸化分離2種類型,混合脂肪酸的分離方式大致分為冷凍壓榨法、表面活性劑法、精餾法等。這幾種方法雖然工藝成熟,但生產條件設備投資要求都較高,生產周期長,有一定污染,產品質量差,未見推廣生產。
我們探索出一套在常溫常壓下能同時生產硬脂酸和油酸的工藝如圖2所示。其中,脫色過程中,白土分3次加入,溫度控制在120 ℃為宜,時間不超過25 min。皂化過程中,皂化溫度保持在100 ℃,皂化時間為4 h,且氫氧化鈉質量分數為8%時效果較佳。混合脂肪酸精制中pH值為8時,Pb(OH)2沉淀相對較少,終硬脂酸純度達到83%。其特點是油酸分離比較徹底,避免了常規工藝中利用熔點不同分離不徹底的弊端,產品品質較好。

03
肥皂和洗衣粉生產工藝
油脂的堿性水解稱作皂化。使用過量的堿,油脂可以完全水解并轉化成脂肪酸鹽和甘油[5]。皂化反應是不可逆反應,其反應方程式如圖3所示。式中:R1 、R2 、R3 分別代表3個碳原子數相同或者不同的烴基。
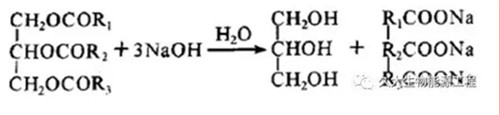
皂化方法有2種:一種為均相皂化;另一種為非均相皂化。均相皂化是先將廢油脂溶解于適當的溶劑中(如,乙醇), 形成均相溶液,然后在堿觸媒的作用下水浴進行皂化反應,加入飽和食鹽水,使固體塊狀皂化物析出;而非均相皂化是在維持廢油脂原形的條件下,直接在堿觸媒的作用下進行水浴皂化反應,加入飽和食鹽水,析出皂化物。采用均相皂化法,產物中溶劑的分離和回收較困難;而采用非均相皂化法,皂化反應速度慢,反應時間較長,但能直接有固體皂化物,且皂化物的分離、干燥比較容易,因此一般非均相皂化應用較多。
常用的非均相皂化工藝為:將一定量的脫色廢油脂加入反應器,水浴加熱至100 ℃時將質量分數為30%的氫氧化鈉溶液分3 次加入到廢油脂中[ m (NaOH) ∶m(廢油脂) = 1∶2 ] ,邊加入邊緩慢攪拌,使油脂與堿液充分接觸。在皂化反應開始時先加入1/4的堿液,攪拌至油脂呈乳化狀態分散在堿液中,時間約1 h,此時皂化反應加快,再加入2/4的堿液,反應2 h后,加入剩余堿液。反應過程中要不斷攪拌,并控制pH值在9~10。當皂粒或皂膠形成后,鹽析2 次,靜置沉淀1 d,排出底部的黑水。皂基逐漸凝固析出,取出干燥后,可壓制成不同形狀的肥皂或配制洗衣粉。
研究表明,餐廚廢油脂的非均相皂化反應時間越長、溫度越高,用堿量越大,廢油脂的皂化度越高。但皂化時間過長和堿用量過大會使皂化物顏色加深,產物膠化。皂化反應的較佳條件是:反應時間4 h ,反應溫度100 ℃,堿液用量(NaOH與廢油脂質量比) 為1∶2 ,皂化用NaOH 濃度為30%。
04
潤滑油生產工藝
利用餐廚廢油作為原料生產潤滑油的工藝如圖4所示。通常分為5個步驟:
(1) 將餐廚廢油、一定量的水、LiOH 和基礎油加入反應器進行皂化。皂化溫度為110~120 ℃。其間反應體系隨著金屬皂的生成粘度增大,不斷補充基礎油,使體系的粘度下降,以便反應能夠正常進行;
(2) 反應進行大約2.5~3h ,體系的粘度不再變化,說明皂化反應完成,可以開始脫水;
(3) 當體系由乳白色變為淡黃色,體系中不再有沸騰的水泡,說明水已蒸干,此時加入剩余的基礎油;
(4) 升溫倒190~200 ℃,體系成為熔膠狀態。停止加熱,進行冷卻;
(5) 冷卻方式對潤滑脂的結構和性能有很大的影響,冷卻方式宜采用自然冷卻(即慢冷)。冷卻至室溫后,用三輥磨進行研磨細碎后,形成潤滑油產品。
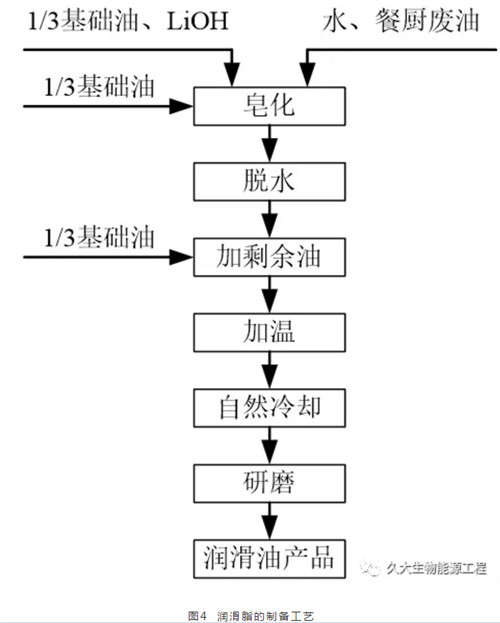
研究發現,由餐飲業廢油脂替代硬脂酸生產制備金屬皂作為潤滑脂的稠化劑是可行的,所得產品的滴點與市售的潤滑脂滴點相近。在制備復合鋰基潤滑脂時,加入草酸復合劑對提高鋰基潤滑脂的滴點非常有效果。癸二酸復合劑對鋰-鈣基潤滑脂的滴點提高較好。
05
混凝土制品脫模劑生產技術
建筑業澆筑混凝土及預制混凝土構件生產時, 混凝土灌注使用模板、模具, 混凝土硬化后應能順利脫模,為克服模板和混凝土之間的粘結力,**混凝土表面光潔,無脫落、粘模現象,在模板或模具表面上常常涂刷一層脫模劑。
長期以來,國內主要采用機油、廢機油、乳化礦物油, 以及皂液、皂化動植物油下腳料等作為脫模劑。礦物油類脫模劑的使用易造成礦物油進入環境,造成污染;皂類、高分子吸水樹脂型礦物脫模劑成膜后, 耐水性較差, 脫模效果受到影響;用餐飲業廢油脂脫模劑可使制造成本大大降低,直接使用油脂涂刷模具, 常常造成油膜過厚, 形成浪費, 附著在模板上的油脂較粘, 新混凝土結構面層的氣泡一旦接觸到粘稠的油膜, 即使合理的振搗氣泡也很難沿模板上升排出, 直接導致混凝土結構表面出現蜂窩麻面。
采用添加乳化劑的方法, 實現脫模劑的自乳化, 即在使用前與水適當混合即可成為相對穩定的乳化液。乳化液涂刷模具可形成較薄的油膜從而實現節約, 并能克服混凝土表面缺陷,因此研制環保混凝土制品脫模劑十分必要。王益民等人研究發現,常壓反應釜加入白油精制的下腳料( 主要成分是石油磺酸),升溫至80℃,加石灰乳中和,反應20min,加入少量脂肪醇聚乙烯醚, 攪拌15min, 即得乳化劑。將乳化劑按6% 比例與餐飲業廢油脂混合, 即成為淺棕色透明油狀產品。使用時將其用水稀釋至8 倍制成乳化液, 即為混凝土制品脫模劑,改脫模劑穩定性好, 脫模性能好, 對鋼模無銹蝕危害。
來源:環衛之聲